The Transformative Power of Automotive Plastic Injection Molding
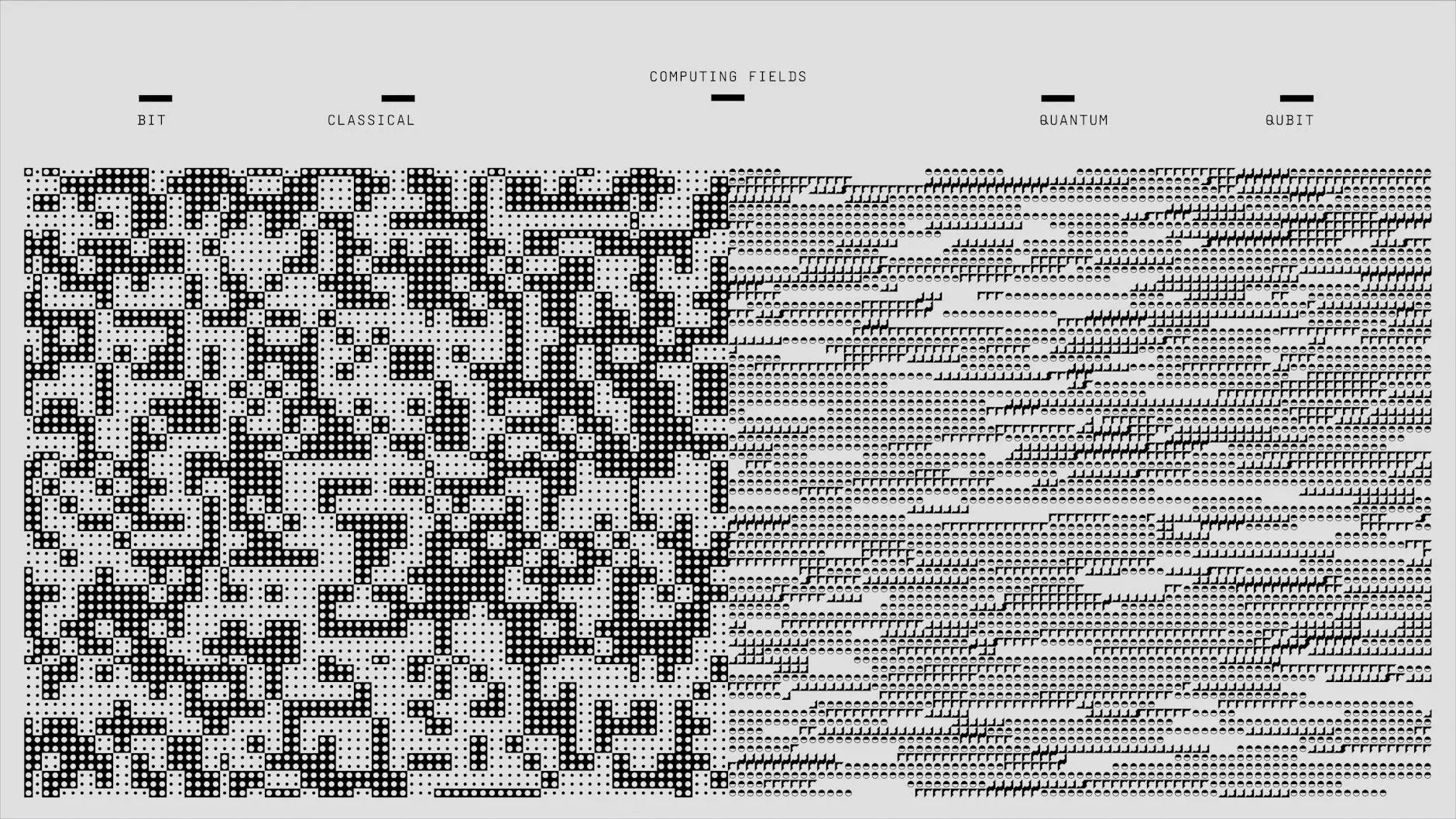
Automotive plastic injection molding is rapidly becoming a cornerstone of modern manufacturing in the automotive industry. With the merging of advanced technologies, innovative materials, and consumer demands for efficient vehicles, the method of injection molding has evolved to meet these challenges head-on.
Understanding Automotive Plastic Injection Molding
At its core, automotive plastic injection molding involves the process of producing plastic parts by injecting molten plastic into a mold. This technique is ideal for creating high-precision components that are critical to vehicle performance. The process has numerous advantages, making it a preferred choice among automotive manufacturers.
The Advantages of Automotive Plastic Injection Molding
There are several notable benefits that make automotive plastic injection molding advantageous:
- Cost-Effectiveness: Once the initial mold is created, the cost to produce each additional part significantly decreases, leading to lower overall production costs.
- High Precision: Injection molding allows for tight tolerances and complex geometries which are difficult to achieve with other manufacturing methods.
- Rapid Production: This method can produce large volumes of parts quickly, enhancing turnaround times in manufacturing processes.
- Material Versatility: A wide range of plastic materials can be used, including thermoplastics and thermosets, which cater to different automotive applications.
- Reduced Waste: With precise material usage and near-complete molding cycles, waste is minimized, supporting sustainability efforts.
- Enhanced Durability: Modern polymers used in injection molding can withstand harsh environmental conditions, ensuring longevity and reliability of automotive components.
Key Applications in the Automotive Industry
The applications of automotive plastic injection molding span a wide spectrum within the automotive sector. Below are a few areas where this technique plays a crucial role:
1. Interior Components
From dashboards to door panels, the interior of vehicles significantly benefits from injection-molded plastics. These components not only enhance aesthetic appeal but also reduce weight, which is essential for energy efficiency.
2. Exterior Parts
Items such as bumpers, grilles, and lighting fixtures are often produced through injection molding. These exterior components must endure a variety of weather conditions, making material selection vital.
3. Functional Components
Functional parts, such as clips, fasteners, and brackets, can be efficiently produced with injection molding. These components must meet specific performance criteria under automotive conditions.
4. Under-the-Hood Applications
Components exposed to higher temperatures and mechanical stresses, such as air intake manifolds and thermostat housings, are increasingly made from advanced injection-molded materials.
The Role of Technology in Injection Molding
Advancements in technology have profoundly impacted automotive plastic injection molding. The integration of:
- 3D Printing: Prototyping components using 3D printing can streamline the design process, allowing for rapid iterations before committing to full production molds.
- Simulation Software: Advanced software can simulate mold filling and cooling, allowing designers to optimize the process and predict potential issues before they arise.
- Automated Systems: Automation in mold making and part removal has increased efficiency, reducing labor costs and speeds up production cycles.
Sustainability and Recycling in Automotive Plastic Injection Molding
The automotive industry is under increasing pressure to adopt sustainable practices. Automotive plastic injection molding facilitates this through the use of recyclable materials and production waste minimization:
- Use of Recycled Plastics: Various manufacturers are producing parts using recycled materials, reducing the plastic footprint.
- Bio-based Plastics: The rise of bioplastics is offering alternatives that are less harmful to the environment, which can also be used in injection molding.
- Closed-loop Systems: Manufacturers are increasingly choosing to implement closed-loop systems where scrap and defective parts are recycled back into the manufacturing process.
Conclusion: The Bright Future of Automotive Plastic Injection Molding
The automotive industry is undergoing significant transformations, and automotive plastic injection molding stands at the forefront of these changes. With its ability to enhance the efficiency of production, reduce costs, and provide innovative solutions for complex components, it is clear why this process is vital for modern automotive manufacturing.
As manufacturers like Deep Mould continue to invest in technology and sustainable practices, the prospects for automotive plastic injection molding look promising. The continued development and application of these technologies will not only meet the growing demands of the automotive market but also contribute positively to environmental sustainability.
For automotive companies looking to stay ahead of the curve, embracing the innovation and advantages of automotive plastic injection molding is not just beneficial—it’s essential for future success.